Traction through a pipe traction down a wire
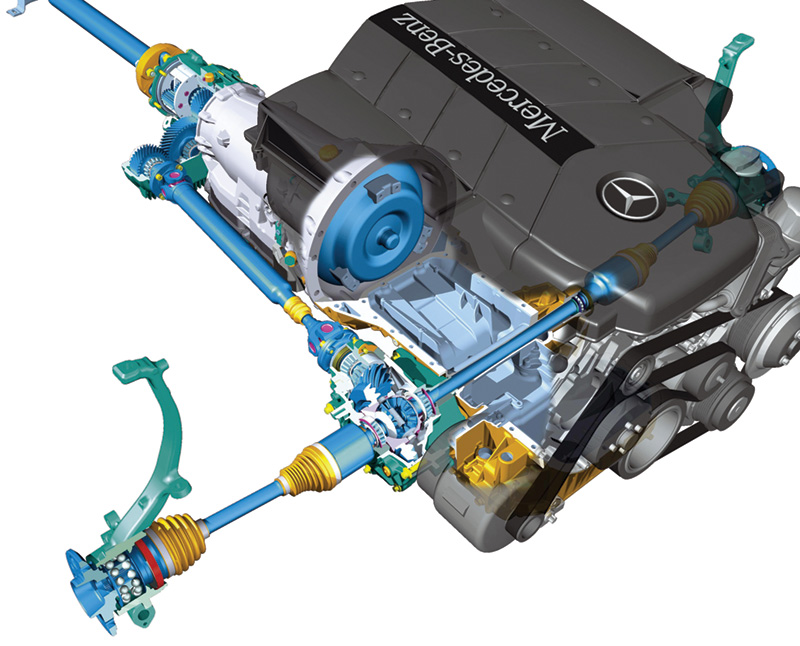
Later nonhydraulic versions of 4MATIC, employing 4ETS, use open differentials front, back and center, with no multidisk clutches at all. They can do this because the later system uses individual wheel brakes to keep individual drivewheels from spinning when their torque exceeds the traction available at that tirepatch. The brakes have the identical effect to that of the multidisk clutches in the hydraulic version: they prevent overspeed of the wheel with less traction. Similarly, there are two-wheel-drive brake-activated drive traction controls analogous to ASD.
Four-wheel-drive increases traction, often enough to sustain movement and control under conditions that might otherwise mean the driver would choose to stop or would get stuck in snow, mud or sand. Four-wheel-drive is not constantly advantageous, however, because it mechanically couples all the wheels and drivetrains together; and sometimes, surprisingly enough, that connection can work against optimization of traction and control. There have been two quite different systems called 4MATIC, the first hydraulic, beginning about 1990 and the second electronic, working through the service brakes, starting in 1998. We concentrate here on the earlier system since you’re more likely to see it in an independent shop.
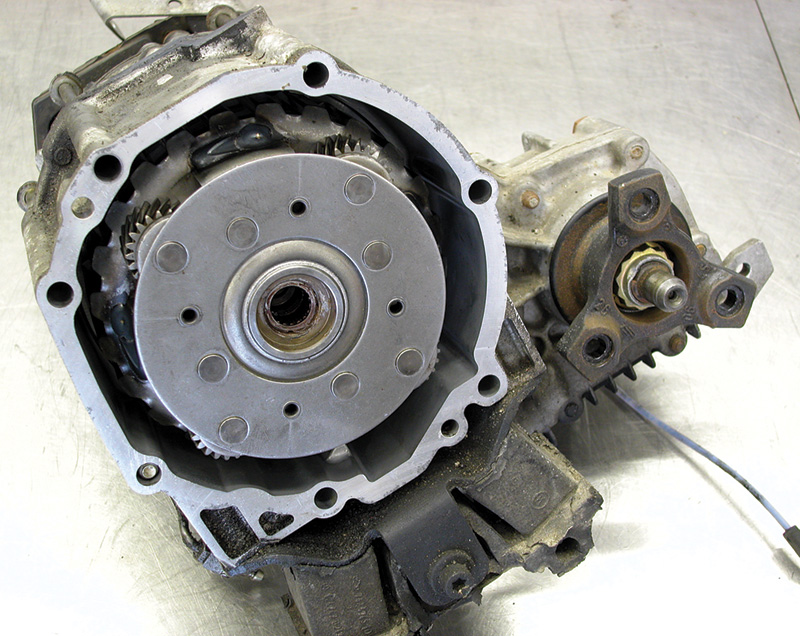
At the heart of the 4MATIC system is the trans- fer case, splitting the torque from the transmission to each of the driveaxles.
Locked and Open Differentials
“Four-wheel-drive” can be a misleading description. In principle, of course, any driveline system conducting power through the transmission to all four wheels is ‘four-wheel-drive.’ There are, however, significant differences arising from the distinction between locked and open differentials. Let’s have that clear first.
The ordinary, familiar differential is an ‘open’ differential. Torque delivered through the driveshaft pinion and differential ring gear applies equally through the spider gears to each axle halfshaft, regardless of individual halfshaft speed. Aside from slight friction between internal parts, an open differential applies equal torque to each axle – with the consequence that the maximum torque the differential can apply to its drivewheels is just double what the drivewheel with less traction can transmit alone, the drivewheel that slips first. Once that first wheel spins, the vehicle stops progress. This is exactly what we see when a car spins a drivewheel in a snowpile or mudhole: Until that wheel regains traction, a stationary car doesn’t budge. In the extremes of limited traction, an open differential gives you one-wheel-drive, and, worse yet, drive through whichever wheel has less traction.
So we move to the locked or limited-slip differential. “Locked” is an exaggeration, as you know, because inside and outside wheels must travel different speeds in a turn. Otherwise the inside wheel, usually less heavily loaded as centrifugal force throws the weight outward, must skid forward along the pavement.
The 4MATIC differentials ‘lock’ in a way similar to the limited-slip differentials you may know from domestic trucks or high-performance (at least fast-acceleration) vehicles. In most of those, a constantly spring-loaded multidisk clutch links the opposite-side axle shafts, through a friction material and special lubricant, both requiring periodic replacement. The earlier 4MATICs use hydraulics to engage the clutches, as we’ll see.
There are also true locking differentials using sliding-dog clutches, but these engage with an immediate, heavy clank, a force reminiscent of excavation or railroad equipment, an engagement force that would be quite unwelcome in a sedan. With an earthmoving implement, this doesn’t matter since the grinding earth moves under the tire lugs and since neither driving comfort nor speed was a priority, anyway. With a sedan, that’s out of the question. On a vehicle driving mostly on hard pavement, you don’t want a truly locking differential, not only because that would abrade the tires with lower load quickly, but also because it would mean one or the other tire on an axle would have to slide in every turn, actually reducing traction even under what should have been ideal pavement conditions.
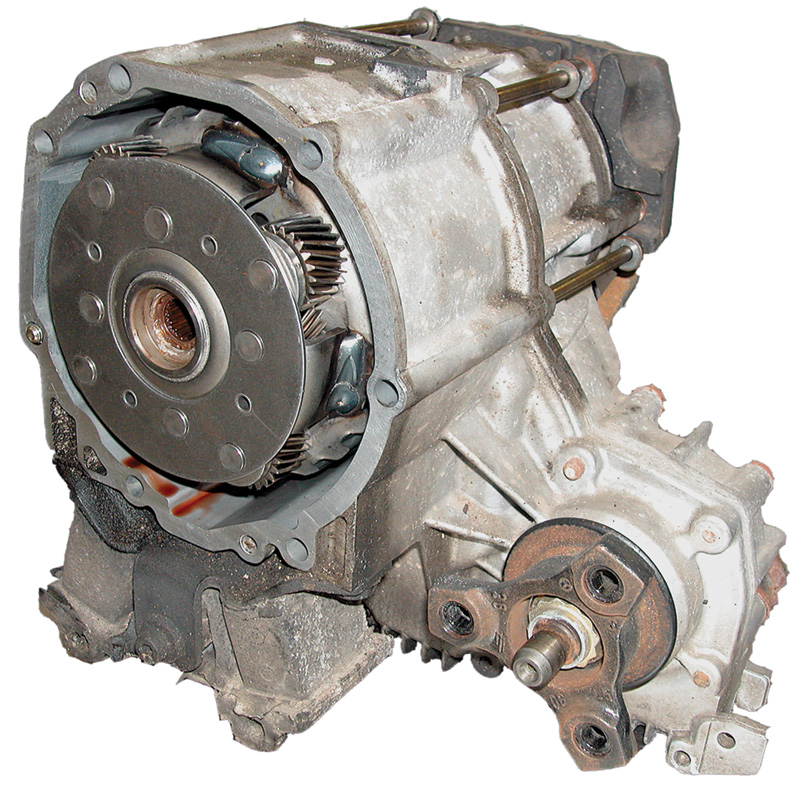
The transfer case can engage two-wheel-drive only, four-wheel-drive or four-wheel-locked. In the last case, front and rear axles turn at the same speed.
Torque through the Transfer Case
The earliest four-wheel-drive systems simply used a second driveshaft from a transfer case to the front axle differential, where another open differential did its torque-splitting work. The same ‘less-traction’ limitation still applies, but with this advantage: The average speed of the front wheels would, by solid mechanical linkage, move at exactly the same speed as the average speed of the rears (“average” because each wheel on each axle can still move at a different speed from its opposite number, but each axle’s differential ring gear turns at exactly the same speed as the other axle’s).
This means two wheels, one on each axle, have to slip simultaneously for the vehicle’s motion to stop. Such four-wheel-drive will, however, represent a significant traction improvement over plain-vanilla two-wheel-drive. After all, it means at least a doubling of traction, and usually more than that, assuming somewhat different traction at each wheel. Just as two-wheel-drive through an open differential really means one-wheel-drive, four-wheel-drive through two open differentials really means two-wheel-drive.
That’s more traction, but it doesn’t use all the traction available.
A four-wheel-drive system that locks the front and rear axles together still has the problem that one axle or the other must slip in every turn, because the front wheels will invariably follow a track along a smaller radius and shorter path than the rears. A long time ago, I had an ancient Jeep that never really got stuck, but took every turn with unpredictable directional excitement anytime four-wheel-drive was engaged. You could never tell whether the front or the rear axle would slide loose sideways first – that depended on everything from the load to the quality of the gravel on the road. And your corrective maneuver had to wait until the slip was clearly underway, because you turned the steering wheel in opposite directions to recover depending on which axle slid. Excitement, as I said.
The obvious manufacturing fix is to include an interaxle differential, which all modern four-wheel-drives do. You can’t just add a center differential and let it go at that, however, or you’re back with your original problem: All the torque goes to the first wheel that slips, and the vehicle stops there. Four-wheel-drive with three open differentials becomes, in the extreme, one-wheel-drive again.
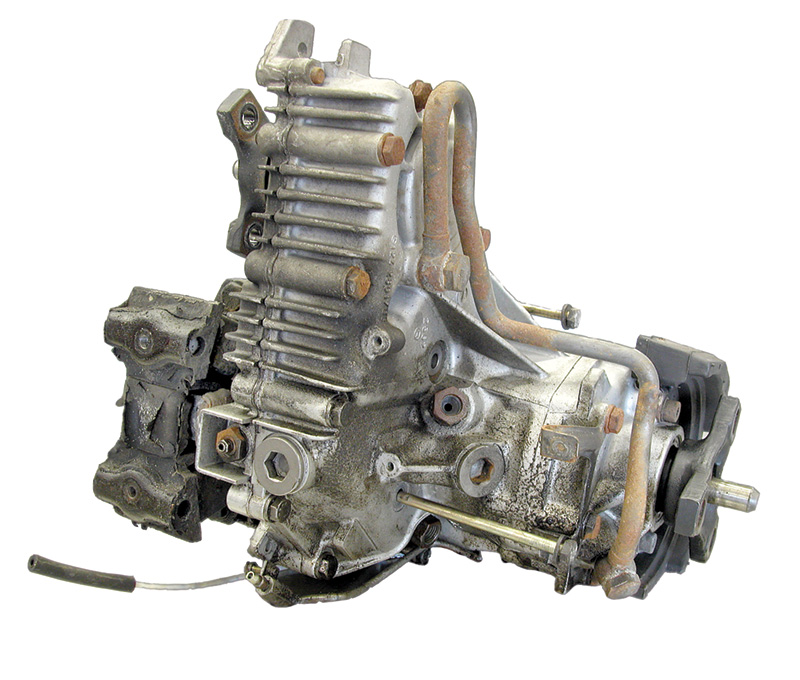
The system works hydraulically, but it’s also internally lubricated with oil. If the seals on the multidisk clutch pistons start to leak, the hydraulic oil can fill the transfer case and begin to run from the vent. The loss of hydraulic fluid would be obvious long before that.
4MATIC Progressive Locks
So the Mercedes-Benz 4MATIC system employs ‘locked’ four-wheel-drive when the various sensors indicate the need for the additional traction, but not under normal driving conditions when ordinary two-wheel-drive through the open rear differential is sufficient to conduct all the forward drive moment the engine can deliver to the wheels, and not under those special driving conditions when – paradoxically – a locked four-wheel- drive could make a low-traction condition worse.
Perhaps the most important such contrary condition occurs during hard-braked, ABS-pulsed stops, particularly in turns. If four-wheel-drive were still engaged under those conditions, it would be possible for the interconnected drivelines either to mask a wheel’s slip from the sensor’s report and thus block the control unit’s recognition and countermeasures, or to force a wheel with limited traction to turn at the same speed as the others (this last is most noticeable during a steep turn or rapid steering changes, when wheelspeed varies at the different wheels because each follows a path with a different turning radius and different length (and thus, a different speed). To accommodate turns, one of the inputs to the 4MATIC control unit is a steering wheel angle sensor, similar but not identical to or interchangeable with the one used with ASR, ESP and ETS.
The greater the steering wheel angle, the larger the speed difference the system allows between the wheels.
4MATIC is the ‘most mechanical’ (thus the ‘Pipe’ of our subtitle) of the Mercedes-Benz traction control systems, because it involves not only all the steel shafts and gearworks of the supplementary front drivetrain and the transfer case, but also a detailed hydraulic system, from pump to actuator pistons, to actuate the various differential locks that come into play under conditions we’ll discuss in a minute. ETS, the new 4MATIC system employing 4ETS, in contrast, works mainly electronically (thus the ‘Wire’ of our subtitle), with the control unit activating specific wheel brakes to keep the wheel with the least traction from spinning. ETS works specifically with two-wheel-drive cars; 4ETS applies to those with a front driveaxle. Somewhat confusingly, 4ETS is also called 4MATIC.
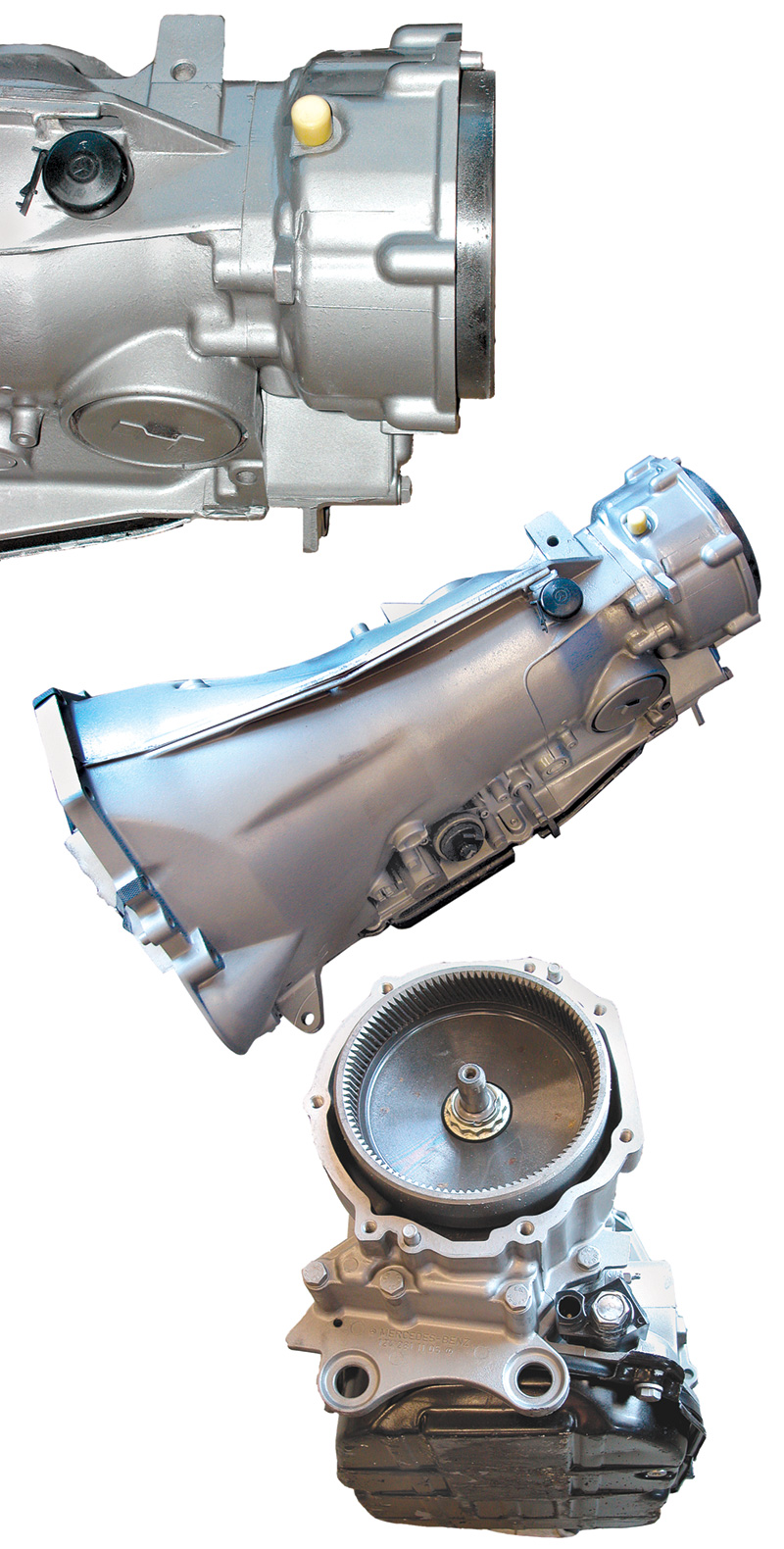
The transmission for 4MATIC is identical to the transmission for the car without that option, however the 4MATIC version includes a ring gear and flange on the output shaft of the gearbox.
Here are the progressive steps 4MATIC employs when the wheelspeed sensors and the steering wheel sensor information point to drivewheel spin: Driving along an ordinary road with good traction and no wheelspin, the car works by ordinary two-wheel-drive with an open differential at the rear drivewheels. This provides the best combination of drive and directional traction in the absence of a problem.
The older hydraulic system provides open-differential two-wheel-drive because the multidisk clutch pack for the center differential lock is spring loaded closed, that is, engaged. This couples the input shaft from the transmission to the transfer case planetary carrier, splined directly to the driveshaft for the rear axle. This is the fail-safe mode of the system, insuring rear-axle two-wheel-drive regardless of any electrical or hydraulic fault in the mechanism.
When the sensors indicate the rear drivewheels are turning faster than the front wheels, at a threshold determined by the control unit as wheelslip, the system switches over to its first shift stage, ‘compensated’ four-wheel-drive. ‘Compensated’ four-wheel-drive is neither an open differential nor one that’s locked. Instead, the geometry of the transfer case gears routes 65 percent of the torque to the rear axle and 35 percent to the front. This allows all four wheels to turn at different speeds, but within plausible constraints of how much traction they might have and how much drive torque they can absorb. The system selects this stage by applying hydraulic pressure to both the clutch packs in the transfer case, unloading the spring-loaded center differential lock and engaging the front axle drive clutch.
The third stage, the second shift stage, locks the interaxle differential by releasing hydraulic pressure to its clutch (allowing the spring to lock it) while maintaining engagement pressure to the front axle clutch. Now we have traction similar to that old
Jeep – it won’t get stuck easily, but a steep turn could be a problem, were it not for the steering angle sensor, which would signal time to return to the previous shift stage. To prevent engine surge, the system briefly engages this stage every time, releasing the center lock shortly thereafter.
The fourth stage, the third shift stage, adds the lock for the rear differential, preventing those drivewheels from turning at significantly different speeds. There is no differential lock on the front axle differential because that could cause a steering problem. Better that a driver gets temporarily stuck than temporarily loses steering.
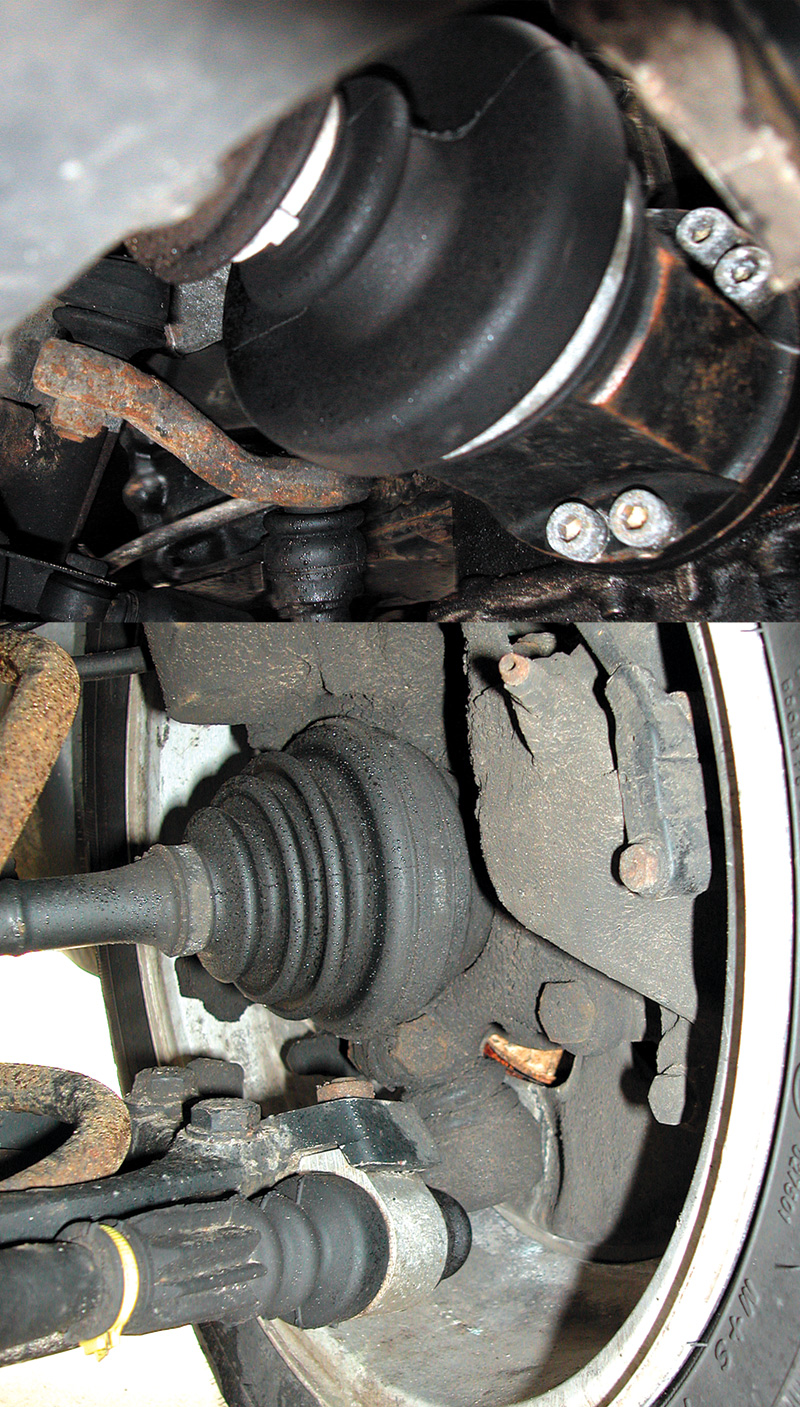
It seems odd to see front-drive components on a Mercedes-Benz, but that’s what comes (in addition, obviously, to the rear drivetrain) with 4MATIC. The front differential shares the oilpan metal housing.
Since the disks don’t mechanically lock, there is still enough difference of speed between the halfshafts to accommodate the difference of speeds in ordinary maneuvers and turns. The system ‘locks’ with a substantial but not excessive resistance to turning at different speeds. There is, in fact, a test you perform with a torque wrench to check the frictional force of the hydraulic ‘lock.’ Specifications vary by model, largely reflecting the weight of the car and its consequent traction. Like any test involving a live drivetrain on a hoist with the engine running, this requires considerable attention to the correct procedures to prevent an accident.
There are three differentials involved in 4MATIC: the familiar one in the pumpkin case at the center of the rear axle, a similar one in front sharing a housing with the oilpan, and a sun-and-planetary design in the transfer case connecting the front and rear driveshafts. There is no locking clutch in the front axle differential, because locking the steering wheels together would destabilize the car during turns. The locking clutch in the rear axle differential is essentially the same mechanism familiar from ASD, which we discussed in an earlier issue. Notice each of these differentials is necessary for all but the most primitive of four-wheel-drive systems. And the Mercedes-Benz system is far from the most primitive.
The interaxle differential does not look much like a differential, but here’s how it works. The transmission for a 4MATIC car is the same as for the others, but the tailshaft ends in a ring gear shell rather than the output shaft and three-lobed driveflange that couples to the driveshaft through the flexible rubber joint (the ‘Gobbo’ joint). The internal teeth of that output ring gear shell engage what initially appear to be the planetary gears on a carrier. Closer inspection, however, reveals a second set of planetary idlers driven by the first set, and these second gears engage the sun gear at the center.
This arrangement of sets of planetary idlers on the carrier is called a “Ravineaux gearset,” and grizzled StarTuned readers long on the job may recall that was the central gearset of the two-speed automatic transmissions long used in domestic automatic transmissions. The reason for using a Ravineaux gearset is that the geometry allows the sun and ring gears to turn in the same direction. The relative sizes of the sun and planetary gears determine the torque split front to rear when the center lock is disengaged.

The 4MATIC hydraulic pump is actually two pumps, the first for the power steering. The same hydraulics also serve the hydropneumatic suspension system, if the car includes that.
Notice this may mean there is still no usable traction. It is much less likely that traction conditions will be so poor that none of the wheels will have sufficient traction to move the car, but that is possible. We can all imagine (and some of us who live in the North have experienced!) conditions under which this is just what happens – all the wheels spin, but the car still can’t move. Like all the traction-control systems, 4MATIC is limited to working in the real world with real-world physical limitations. It works very well, but not magically.
Working with 4MATIC
Here are some service points when working on a 4MATIC car. As with any hydraulic system, air bubbles and leaks sometimes occur. You can often flush air through the system by merely toggling the service valve forward to the test position and running the engine. This opens the circuits and lets the oil flow. If there is still air in the system, you can vent it from the caps on the rear differential pistons and by loosening the hydraulic lines at the transfer case until the oil flows clear – usually only a few seconds. By anecdote, the most common part requiring replacement is the pump, but this is probably because the pump is the high point in the system and loses lubrication first if there’s a leak. This tandem pump forms a unit with the power steering system and also provides hydraulic pressure for any vehicle with hydropneumatic suspension.
The accumulator, a compressed nitrogen chamber atop the hydraulic control unit, includes a diaphragm to separate gas from oil. If that diaphragm eventually leaks, the accumulator can cease priming hydraulic components and can allow the system to make periodic ‘water-hammer’ clunks as the pump cycles. If the noise goes away with the service valve in the test position, suspect the accumulator.
A mechanical problem that may set you to scratching your head comes if you remove the front driveshaft. With the rear driveshaft, you can bend it in the middle at the center bearing to shorten it and remove it from the car. But there is no joint in the short front driveshaft. Instead, you pull back the rubber boot at the front, loosen the locking cap and slide back the splined coupling. Pay close attention to centering the shaft in the flexible joints on reassembly, or you could have a running noise that will be very hard to diagnose. Match-marking the parts with chalk or paint is a reasonable precaution.
Traction by Wire
ETS and its multi-axle analog, 4ETS, are simpler, electronic variants of ASD and the earlier hydraulic 4MATIC. The simplification comes from the absence of the hydraulic distributor-lockup components involved in ASD and 4MATIC. Don’t be misled, however, there is still plenty of hydraulic work afoot – but through the brake system. Instead of controlling wheelslip by locking one or more differentials, ETS selectively actuates the brake on whichever drivewheel slips. Not all ETS cars have four-wheel-drive, but those that do employ plain open differentials all around, counting the unclutched sun-and-planetary in the ETS transfer case as plain and open.
Such traction increase must obviously toggle on and off very rapidly, as fast as the driving conditions
change. This is possible only with a digitally controlled automatic system, one that works directly from sensor inputs rather than just from driver controls. The driver, after all, has many other tasks to perform.
Like ASD, this could mean there would still be drivewheel slip if there were more delivered engine torque than the available traction could employ. In such a case, both drivewheels would slip, not just the one; but a driver with any level of awareness of driving dynamics should have noticed the problem and lightened his foot. To encourage development of this awareness, the instrument panel includes a warning lamp that the system is at work retaining traction, and that the driver should accommodate his expectations to the physics of the available wheelpatch-to-pavement friction.
ETS works in ways quite familiar to people who know ABS, ASR and ESP. Preventing drivewheel spin by applying the wheelbrake, in fact, could be marginally more effective than locking a differential, since the system could control all four wheels at different speeds effectively. With the open front differential, the older, hydraulic 4MATIC cannot do that.
0 Comments