The best rotors in the world will soon come back with a pulsation problem if mounting errors produce even a small amount of wobble.
Providing customers with premium brake service goes beyond replacing worn out friction materials. It includes restoring all aspects of the Mercedes-Benz brake system to like-new operation. A working knowledge of disc thickness variation (DTV) issues generated by runout, along with indexing and other techniques for minimizing runout, are proving to be critically important for techs in minimizing comebacks for brake pulsation complaints.
Consumers and technicians alike refer to rotors with disc thickness variation (DTV) as “warped.” What is often misunderstood is that DTV, and resultant brake pedal pulsation or“judder,” is a symptom of excessive runout.
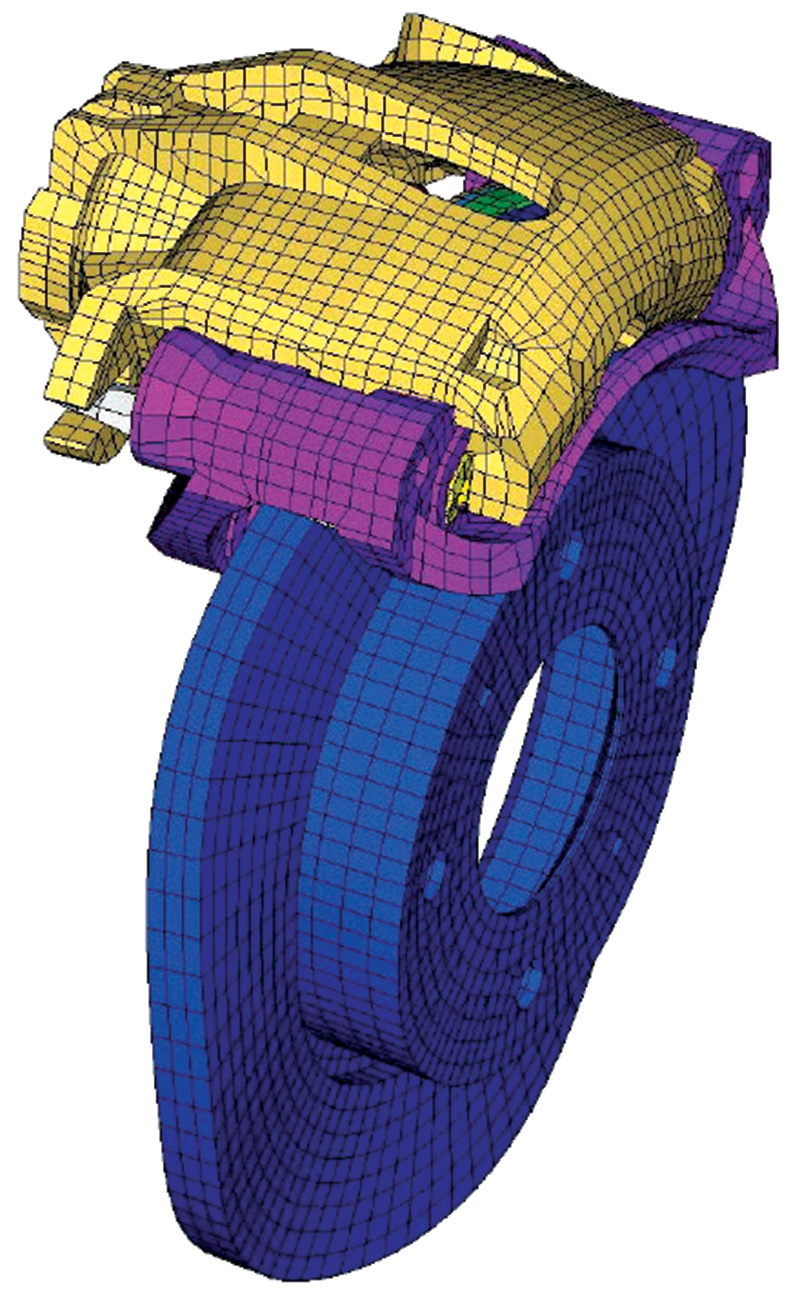
A wavy rotor will develop DTV because certain spots will contact the pads on every revolution, which will make those areas thinner.
How Runout Creates DTV
The general public as well as many techs blame brake judder on “warped discs.” The truth isn’t quite so simple. At least in theory, a wavy or “perfectly” warped rotor would be the same thickness in all spots, and a floating caliper would simply follow it as it tracked from side to side. In practice, a warped disc, or a disc that doesn’t sit completely flat on the hub will contact the caliper at its high spots, but not the low spots. Constant rubbing leads to the creation of thick and thin spots on the disc. The caliper piston(s) follows these variations in and out, pushing fluid back against the pedal, creating the all-too familiar brake pedal pulsation, or judder. Hence DTV, or “disc thickness variation” is the actual cause of brake judder, not “warped” rotors.
The sources of runout are the stacked tolerances of the hub, mounting faces, and rotor. Turning or replacing “warped” rotors may not sufficiently reduce runout to prevent a brake pulsation problem from returning, although use of an on-car brake lathe can sidestep the problem.
Comebacks for noise issues are hard enough to prevent, but if a vehicle comes back in just a few thousand miles with brake pulsation because of runout issues that weren’t addressed, the owner isn’t going to be happy, and profits may very well go down the drain. Frequent pulsation comebacks more than justify the additional time and effort required to measure and correct for runout the first time around.
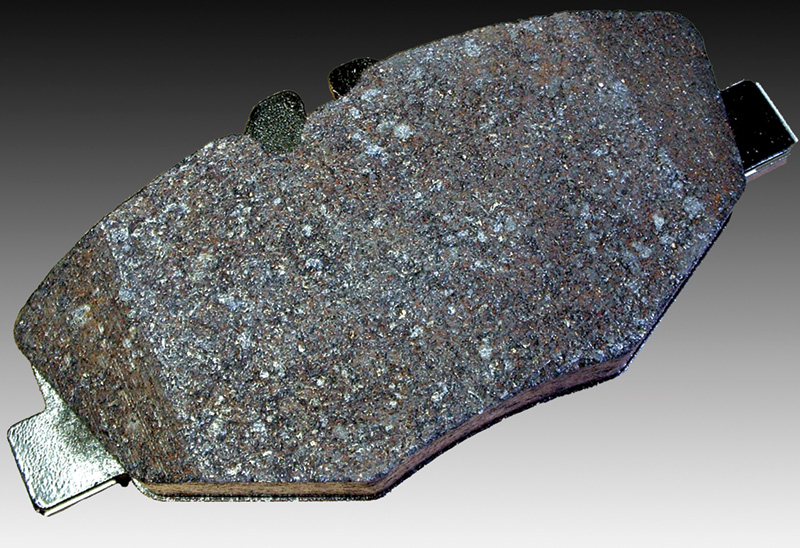
Genuine Mercedes-Benz O.E. replacement linings are formulated to provide the highest possible braking performance. These aggressive friction material recipes, however, do take a toll on rotors, so DTV can develop fast.
So what is runout exactly, and how can technicians correct it to prevent comebacks? Simply stated, runout is the amount of wobble, or side-to-side (lateral) motion, measured on a disc that’s rotating in a horizontal plane. It’s typically measured using a dial indicator attached to Vise-grips, mounted on the steering knuckle or some other solid point.
Rotor runout is a “stacked” tolerance with the wheel bearings, bearing installation inside the hub, hub, rotor hat “face” and rotor disc all potentially contributing to the total.
Root cause
Bearing wear, accident damage (“curb checking”) and corrosion on the hub face all have the potential to cause runout and resulting DTV. Bearings not adequately snugged down, or not pressed absolutely flat into the hub could generate significant runout. Manufacturers of hub-mounted versus caliper-mounted brake lathes argue the relevance of wheel bearing preload to runout.
Rust on the face of the hub where the rotor mounts is probably the leading cause of runout. Iron combines with oxygen to form rust, which takes up sixteen times the space that iron itself does. Just like a tree root lifting a concrete sidewalk, rust in a pitted hub surface, or the back of the rotor “hat” can lift the rotor off the hub even with the lug nuts securely snugged down. This will, of course, cause runout.
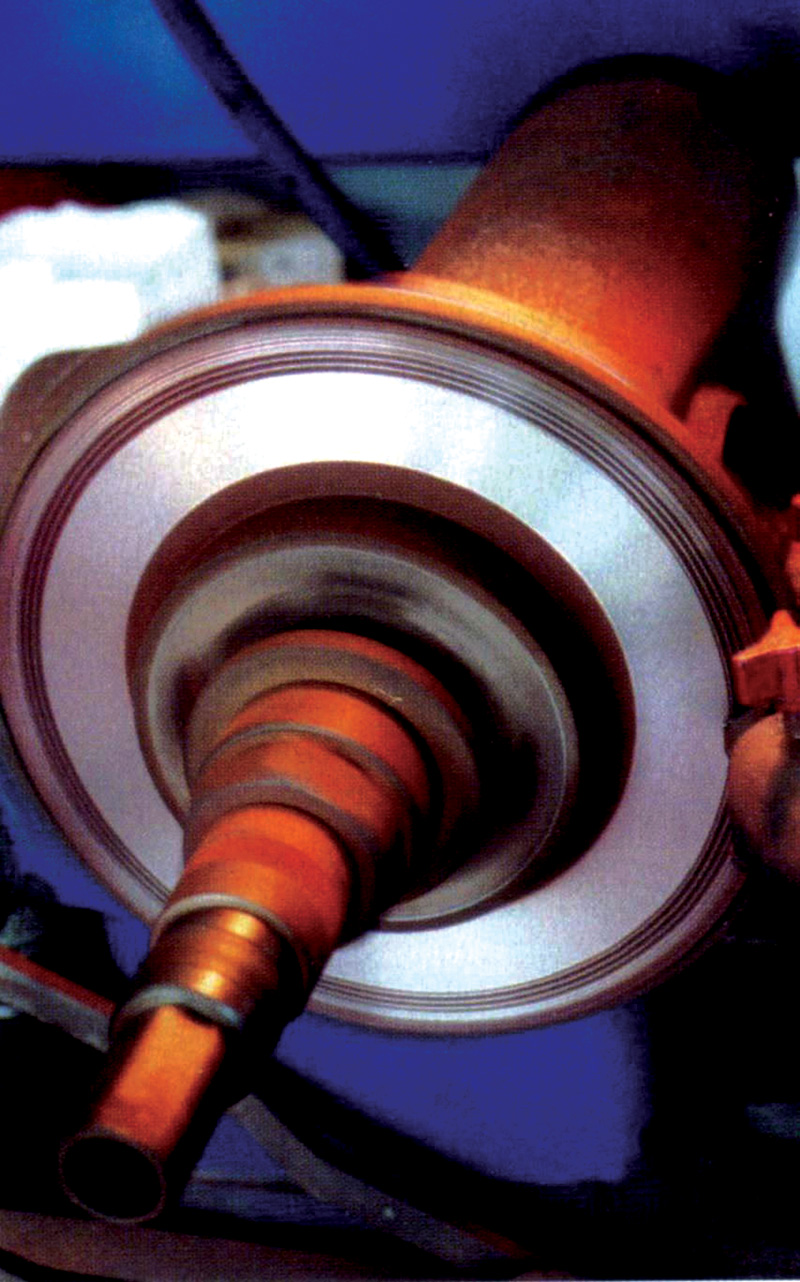
If you are turning rotors to eliminate pedal pulsation,you must make sure you mount them on the lathe arbor perfectly.
There are other potential sources of runout. A bent arbor on a brake lathe can machine rotors that are beautiful to look at, but become ugly when measured using a dial indicator. The same result can occur if the center hole, flange, and/or face of a rotor aren’t adequately cleaned of rust before it gets mounted on a lathe.
Unequally torqued lug nuts can generate as much as .003 in. of runout, another good reason to use a torque wrench to tighten lugnuts.
As They Say in German, “Wieviel ist Zuviel?”
How much runout is too much? In other words, how much will generate DTV? The answer is that it depends on the vehicle. The lighter the car, and the less unsprung weight, the more prone it may be to DTV and brake pulsation. Certain models are known for being more sensitive than others. In general, manufacturers are calling for .002 in. or less runout, measured near the edge of the rotor disc, and .0015 in. on more sensitive models.
How do we properly measure runout? A dial indicator clamped to the steering knuckle is the right tool, but where on the face of the disc should we place the indicator’s tip? One tapered shim vendor states 1/2 in. from the outside edge of the disc. Another authority says 5mm from the edge, and yet another says, “In the middle of the path the pad travels.” The closer to the edge one measures, the greater the reading will be. Clearly, you don’t want to measure runout on the rough, corroded ring beyond the contact area of the lining, but doing it somewhere along the outer third of the path the pad travels won’t get you into any trouble.
Measuring rotor runout requires securing the rotor to the hub using a minimum of three lug nuts. You’ll usually need spacers or washers. In theory, the lug nuts should be torqued the same as if the wheel itself were mounted. Since the car is no longer on the ground, snugging may be challenging, since applying the brakes during tightening could prevent the rotor from self-centering on the hub. Snugging them finger-tight, then jiggling the rotor may help you to center it before the final tightening.
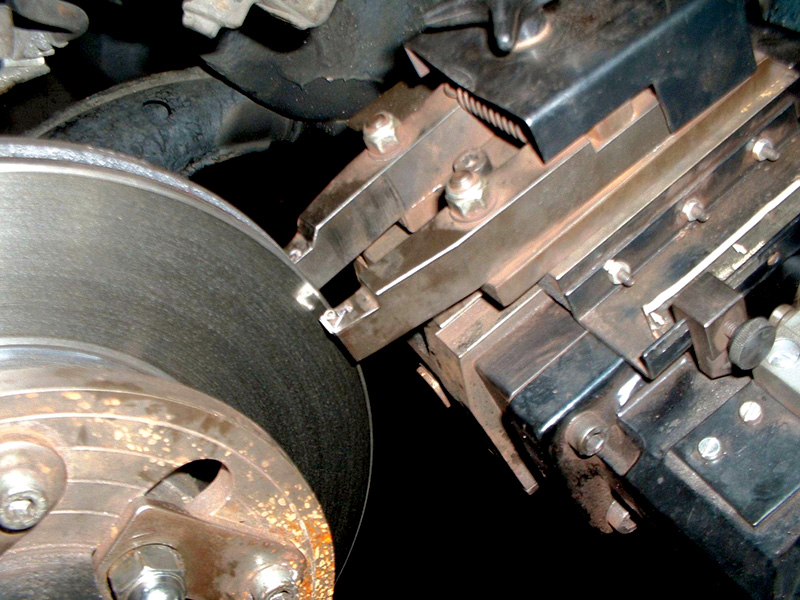
Although an on-car brake lathe can eliminate runout and DTV, you still haven’t addressed the mounting error. So, there’s apt to be trouble at the next reline.
On-car Brake Lathes
Eliminating the potential addition of runout caused by removing and re-installing rotors on rusty or otherwise imperfect hub flanges has led several manufacturers to insist on the use of an on-car lathe whenever techs address pulsation problems for warranty repairs. Mercedes-Benz, however, expects the technicians who are servicing its vehicles to be craftsmanlike enough to make sure nothing interferes with hub mounting perfection, so doesn’t have this requirement. Still, this option can be used to correct stubborn problems, as we’ll explain.
The setup of most on-car lathes incorporates a step where existing runout is measured, and compensated for by the tech prior to cutting. The latest models from Pro-Cut International and others, use a microprocessor-based system to compensate for runout automatically. As a result, rotor indexing, shimming, hub cleaning, and all of these other steps are avoided, provided the rotor has enough “meat” left to allow resurfacing.
Yet, all rotors will eventually have to be replaced. So the solution is for techs to understand the causes and cures of runout rather than solely relying on the use of an on-car lathe every time the problem appears. Without such an understanding a tech would have to cut every brand new rotor on the car simply to correct for runout in the hub itself that gets “stacked” out to the rotor.
Correcting Runout: Hub Cleaning, Indexing, and Shimming
There is a variety of techniques for cleaning up a hub, depending on how badly rusted it is. Simple wire brushing and “zipping” with a Scotchbrite pad will often suffice. Since Mercedes-Benz vehicles use lug bolts instead of wheel lug studs, cleaning the mating surface is relatively easy. If the hub is corroded badly enough, it may require replacement. One manufacturer markets a miniature sandblasting booth for cleaning up heavily rusted hubs. It incorporates a drawstring curtain to prevent abrasive dust from getting where it shouldn’t. If a hub is that bad, consider replacing it.
After cleaning up the hub and rotor mating faces, should you apply anti-seize to prevent future rusting? Some authorities say it’s unnecessary, while others recommend the application of a small amount of a high-temperature, nickel-based anti-seize compound. We tend to agree with the latter opinion, although you can go that one better by spray painting with a rust-resistant coating, such as zinc-rich primer. Just make sure you don’t overdo it so that there are large drips or lumps of paint that could interfere with mounting, or a thick coating that might impede heat dissipation.
Every hub and bearing set has some lateral runout. If the hub has tapered roller bearings, they may need to be snugged to minimize bearing-created runout. In general, runout originating from the hub is something you will measure, and attempt to reduce rather than eliminate altogether, which may be nearly impossible.
If de-rusting the rotor bevel and hub doesn’t reduce runout to under .002 in., try indexing the rotor from one lug position to the next. After measuring the runout and removing the rotor, if you measure the hub runout as well, you can attempt to match up the high and low spots. This “matching” is often performed at the factory when hubs and rotors are initially assembled, so if this is the car’s first brake job, you should definitely make index marks either with a punch or paint so you can put the rotors back on in the original position.
If cleaning and indexing fail to achieve the desired result, the final corrective action available to techs is to install tapered shims. A variety of manufacturers offer rotor shim kits. If shims are already present, they need to be replaced with new ones. Before removing them, however, mark how they were oriented to save time should re-shimming still be required after rotor service or replacement.
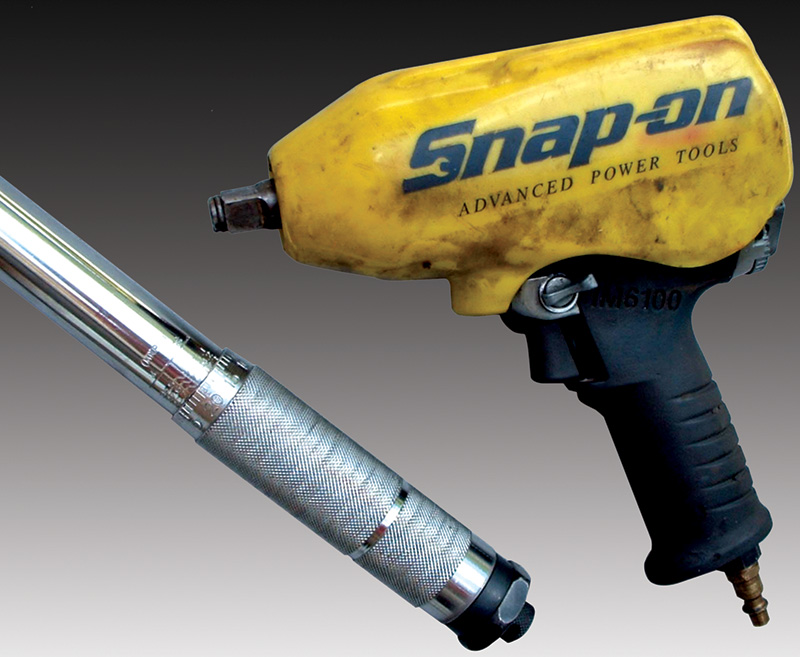
Always use a torque wrench for final lug tightening. Never use a 1/2 in. drive impact gun at all. Spin them down with a 3/8 in. drive tool on a low setting.
Lug Nut Tightening Procedures – Revised!
Most experts agree that in order to prevent lug nut-created runout, wheel installation procedures should be improved. They recommend adding an intermediate tightening step of torquing each nut to half of spec before cinching each down to its final torque setting, as always following the proper tightening pattern.
Using a lower-powered, 3/8 in.-drive impact gun, pneumatic or electric, to spin the nuts down lightly will allow you to add this step to wheel installation without slowing down the operation. Never use your 1/2 in.-drive impact for final tightening — grab that torque wrench!
Summary
Premium brake service consists of more than just restoring how well a vehicle stops after brake service is performed, and preventing irritating noises. It also includes making sure how well every component in the brake system works, as well as how long it will continue to work.
For example, if worn caliper pins aren’t replaced and various sliding components adequately cleaned and properly lubed, new pads won’t wear evenly. Excess brake dust left behind can quickly contaminate lube on shoe or pad motion points. “Weeping” cylinders that are ignored can quickly ruin an otherwise good brake job. Virtually every component in the brake system that isn’t cleaned, lubed, or replaced as necessary during brake service has the potential to lead to comebacks, future brake problems, or to reduce brake life. There’s even the frightening possibility of brake failure.
Despite the high potential for pedal-pulsation comebacks, runout remains unmeasured and uncompensated for at many shops mostly because of the additional time and complexity it adds to performing brake service. This is an unwise shortcut that will typically lead to unhappy customers and complications in the shop’s schedule when the job has to be done a second time.
0 Comments